CXMG 350
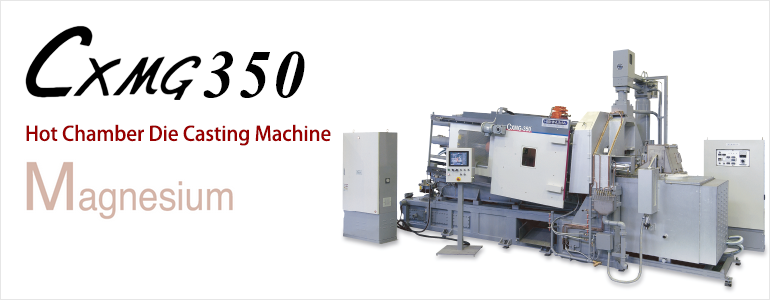
Features of CXMG350
Suitable for big size high precision casting of Laptop computer body and automobile components.
Adapting big volume accumulator. it makes constant quality.
The space between tie bars up to 600×600mm and high strength body, it makes long term stable casting.
CXMG Series Features
Advanced magnesium hot chamber die casting machines serialization.
Excellent stability and durability which enabled prolonged high cycle casting continuously.
Standard equipped multi-language touch panel and piston type accumulator.
Maximum injection speed realized 6m/sec by dry shot.
STANDARD
▶ High-speed injection equipment | ▶ Nozzle touch cylinder |
---|---|
![]() Logic valve and piston type accumulator on the higher speed injector enable constant injection and product quality. Maximum injection speed 6m/sec by dry shot achieved. |
![]() By shifting the nozzle touch cylinder at the operation side and helper side, it improved the maintenance works around injection nozzle. |
▶ Withdrawal ShikiToru flash furnace | ▶ Multilingual touch panel display |
---|---|
![]() Drawer type melting furnace, it makes heating element exchange work be easy. |
![]() Standard equipped multi ‒ language TFT touch-panel display. (Japanese, English, Chinese, Korean, Thai) |
OPTION
▶ Injection waveform monitoring device | ▶ Clamping force display |
---|---|
![]() Displays injection wave(position, speed and pressure), and grasp of relevant casting conditions. |
![]() Displays the die locking force digitally. When die locking force was except a rated value, the safety circuit works to stop the injection. |
▶ Nozzle heater | ▶ Gooseneck heater |
---|---|
![]() Improves working environment by heating a nozzle equally, and it makes stable casting. |
![]() Since a gooseneck is heated with a heater, it contributestoimprovementinwork environment and prevents gas entering into a furnace, also leads to reduction of an oxide. |
▶ Hydraulic jack-up system | ▶ Motor drive safety door |
---|---|
![]() The central hydraulic jack up system allows easy injection position changing. |
![]() The motor-drive safety door reduces the failure rate of long duration operations and shorten the door opening / closing time. |
▶ Sub-plate |
---|
![]() By attaching the exchangeable steel plate to platen, it is reduction of the maintenance cost. |
Peripheral equipment
▶ Hydraulic automatic clamp | ▶Ingot preheating automatic insertion equipment |
---|---|
![]() Hydraulic mold clamping, it can easy to mold exchange safely in a short time. |
![]() The preheated ingot is supplied automatically, it can easy to control the metal level. |
▶ Mold temperature controller |
---|
![]() Management of mold temperature is indispensable to mass production of high precision products. |
Technical Data
Die locking force | kN | 3500 |
Space between tie bars | mm | 600×600 |
Die stroke | mm | 500 |
Die height | mm | 300~700 |
Injection force | KN | 164 |
Injection stroke | mm | 230 |
Injection position | mm | 0/-150 |
Ejection force | KN | 191 |
Ejector stroke | mm | 120 |
Nozzle touch force | KN | 70 |
Nozzle touch stroke | mm | 400 |
Injection plunger diameter | mm | Φ80/90 |
Casting pressure | MPa | 32/25 |
Casting area (efficiency 100%) | cm2 | 1093/1400 |
Maximum shot weight (efficiency 75%) | kg | 1.56/1.97 |
Dry cycle time | sec | 6 |
Working pressure | MPa | 14 |
Oil tank capacity | L | 600 |
Melting pot capacity | kg | 600 |
Electric motor capacity | kw | 22 |
Power supply capacity | KVA | 35 |
Output of electric furnace | kw | 81.6 |
Machine weight | ton | 18 |
The above specifications may vary depending on the model.
Please note that the above specifications are subject to change without notice.